- Introduction to Single Stage Fire Pump: Purpose and Industry Standards
- Understanding Single Stage Centrifugal Fire Pump Technology
- Critical Data: Performance Metrics and Efficiency
- Leading Manufacturers: Comparative Data Table
- Custom Solutions: Configuration, Installation, and Maintenance
- Application Cases: Real-World Integration and Achievements
- Conclusion: Why Choose a Single Stage Fire Pump for Your Facility
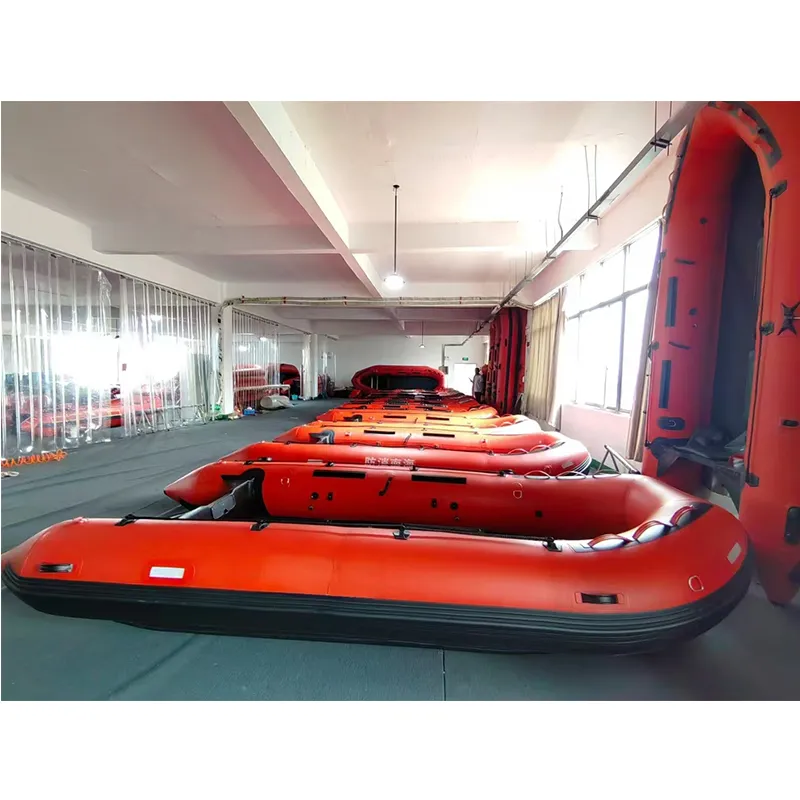
(single stage fire pump)
Introduction to Single Stage Fire Pump: Purpose and Industry Standards
Fire protection systems are crucial assets for safeguarding lives and infrastructure in residential, commercial, and industrial environments. Among the wide range of firefighting solutions available, the single stage fire pump
stands out for its reliability, operational simplicity, and effective pressure generation capabilities. Regulated by stringent international standards such as NFPA 20 and EN 12845, these pumps serve as the backbone of countless facilities' fire suppression systems. With the global fire pump market projected to surpass USD 2.5 billion by 2030, driven by rapid urbanization and industrial expansion, the demand for robust and energy-efficient single stage fire pump solutions has never been higher.
Understanding Single Stage Centrifugal Fire Pump Technology
The performance and popularity of the single stage centrifugal fire pump are rooted in its straightforward engineering. It employs a solitary impeller to accelerate water flow, transforming mechanical energy into hydraulic energy, which is then delivered at high pressure directly into the fire suppression system. This design ensures consistent flow characteristics while minimizing mechanical complexity and maintenance requirements. Compared to multi-stage counterparts, single stage pumps are lauded for their cost-effectiveness, make-and-break reliability, and rapid fire response capability. Advanced mechanical seals and high-quality bearings further enhance operational lifespan, often exceeding 20,000 running hours before major overhaul is needed.
Critical Data: Performance Metrics and Efficiency
Selecting the appropriate fire pump requires a close analysis of key parameters: flow rate, head, horsepower, energy efficiency, net positive suction head (NPSH), and operational footprint. Modern single stage fire pumps are designed to provide discharge pressures between 60-230 psi with typical rated flows ranging from 250 to 2,500 GPM. Their power consumption, when using high-efficiency motors and impellers, can be reduced by up to 12% compared to legacy systems. Furthermore, single phase fire pump variants have emerged for smaller facilities and temporary firefighting solutions, offering ease of installation and standard voltages of 220-240V. Below is a summary of typical technical performance:
Model | Rated Flow (GPM) | Max Head (psi) | Efficiency (%) | Power (kW) | NPSH Required (m) |
---|---|---|---|---|---|
Type A (Standard Single Stage) | 500 | 120 | 78 | 37 | 3.0 |
Type B (High-Efficiency Single Stage) | 750 | 155 | 85 | 55 | 2.4 |
Single Phase Portable | 250 | 100 | 75 | 15 | 3.2 |
Multi-Stage Reference | 500 | 240 | 72 | 44 | 4.2 |
Leading Manufacturers: Comparative Data Table
The global market for fire pumps is dominated by several established manufacturers, each offering specialized designs and technology enhancements for single stage centrifugal fire pumps. Selecting a supplier is often a matter of evaluating product certifications, material of construction (such as cast iron or stainless steel), warranty terms, and regional support. The following table presents a comparative look at leading brands:
Manufacturer | Model Range | Certifications | Warranty (Years) | Material | Global Support |
---|---|---|---|---|---|
Patterson Pump | 350 - 2,000 GPM | UL/FM, NFPA 20 | 2 | Ductile Iron | Yes |
Grundfos | 150 - 1,500 GPM | EN 12845, FM | 3 | Stainless Steel | Yes |
Ebara | 300 - 1,800 GPM | UL/FM | 2 | Cast Iron | Yes |
Pentair | 250 - 2,500 GPM | UL/FM, NFPA 20 | 3 | Ductile Iron | Yes |
Xylem | 400 - 2,300 GPM | UL/FM | 2 | Stainless Steel | Yes |
Buyers should assess not just headline performance, but also after-sales service, replacement part availability, and on-site installation support – critical factors for large-scale installations or remote environments.
Custom Solutions: Configuration, Installation, and Maintenance
Every fire pump system should be tailored to the facility’s unique hazards and operational requirements. Customization begins with pump sizing – ensuring the selected single stage fire pump delivers the stipulated flow and pressure for the installed sprinkler or hydrant system. Clients may specify vertical or horizontal pump orientation, electric or diesel drives, and key features such as variable frequency drives (VFDs) for redundancy and optimal operation.
Installation best practices include vibration isolators, alignment checks, priming instrumentation, and fire-rated enclosures. Routine maintenance is imperative: manufacturers recommend quarterly inspection of seals, bearings, alignment, and impeller clearance. Employing a predictive maintenance approach using IoT-enabled vibration and temperature sensors can reduce unplanned failures by up to 28% according to industry surveys. Properly configured, modern single stage centrifugal fire pumps typically boast a mean time between failures (MTBF) exceeding 4 years with routine care.
Application Cases: Real-World Integration and Achievements
Single stage fire pumps are deployed worldwide across a diverse array of sectors. For instance, a leading logistics center in Singapore implemented a single phase fire pump for its compact warehouse, realizing a 30% reduction in installation labor versus three-phase alternatives and meeting all statutory fire code requirements.
In a North American refinery, upgrading to a high-efficiency single stage centrifugal fire pump improved fire suppression response times by 16 seconds over the previous system, directly attributing to enhanced personnel safety. Simultaneously, a university campus in Europe capitalized on a tailored solution: integrating redundant single stage units with backup power supplies, achieving 99.98% system uptime over three years of operation.
Such cases underscore the flexibility and dependability of these pumps in both new construction and retrofit projects, solidifying their reputation as the go-to choice for mission-critical fire protection.
Conclusion: Why Choose a Single Stage Fire Pump for Your Facility
When determining the optimal firefighting system, organizations require technology that blends uncompromising performance, sustainability, and compliance. The single stage fire pump, leveraging decades of proven reliability, offers precisely this balance. With advanced engineering for higher efficiency, robust certifications, and seamless customization options, it stands as an exceptional choice for a wide spectrum of applications—from small commercial premises to sprawling industrial complexes.
Industry data consistently demonstrates that investments in modern single stage centrifugal fire pump systems can yield lower total cost of ownership, quicker response times, and safer, code-compliant operations. As the demands on fire safety infrastructure continue to rise, decision-makers should prioritize such robust, versatile, and support-backed solutions for sustained asset protection and peace of mind.
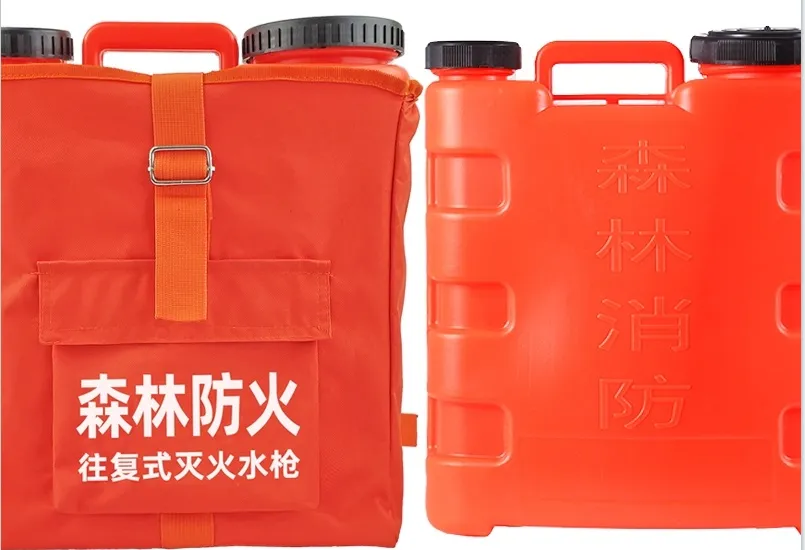
(single stage fire pump)